Stainless steel grades for corrosive environments
Hot alkaline environment
In the alkaline environment of pulp mills, uniform corrosion is the typical corrosion mechanism. Laboratory tests and industry experience have shown that lean duplex grades perform well in these conditions. Surprisingly the “acid proof” molybdenum alloyed stainless steel grades like 316L suffer from rapid deterioration. In addition, duplex grades show superior stress corrosion cracking resistance in alkaline environment compared to 304L.
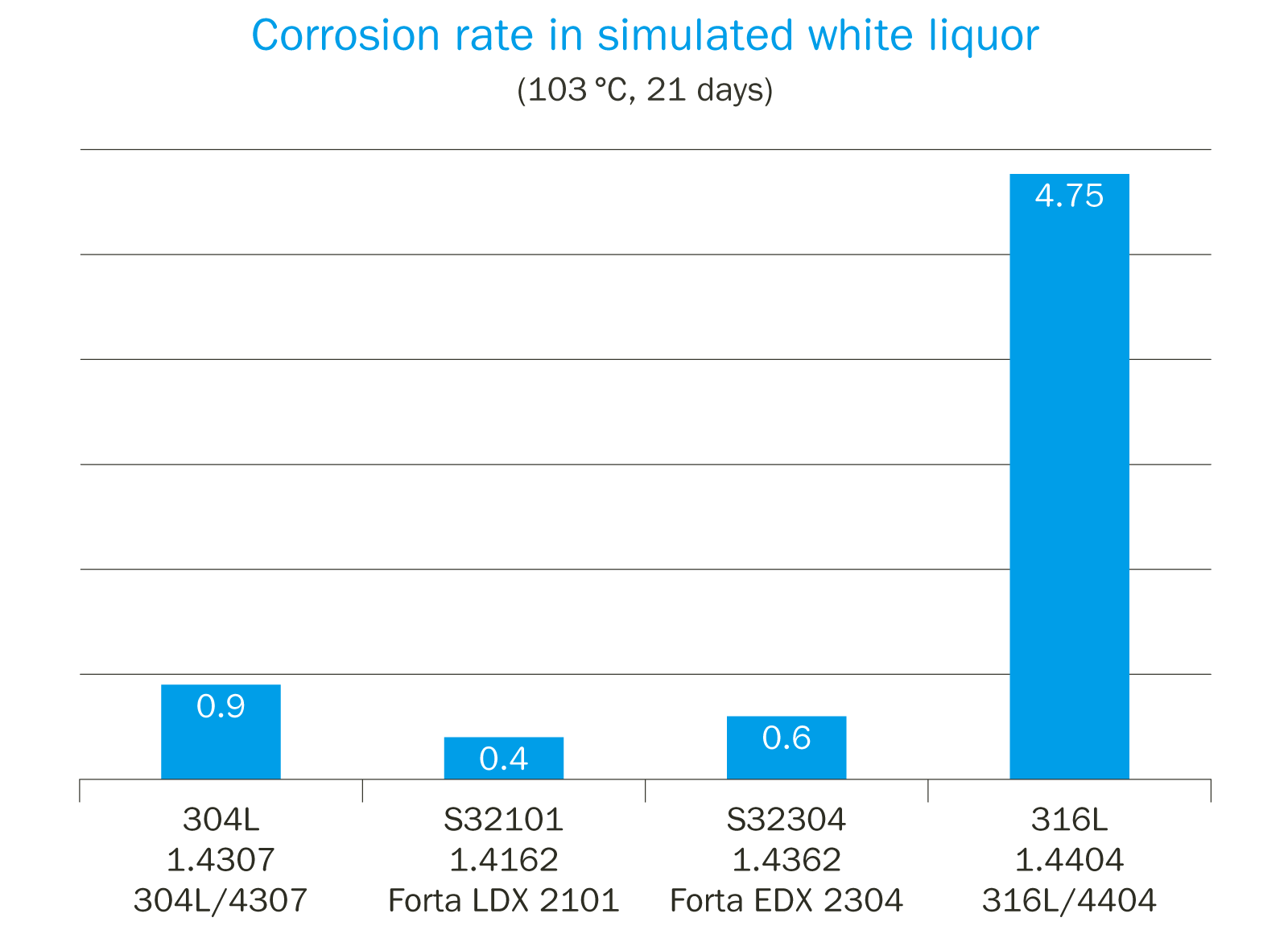
Figure: Corrosion rate test results in simulated white liquor at 103⁰C for 21 days
Acidic chlorine environment
In an acidic chlorine environment, the key in improving the corrosion resistance of stainless steel is increase in alloying content of chromium, molybdenum and nitrogen. With that in mind, austenitic high-alloyed grades like
Ultra 254 SMO and
Ultra 904L are well suited to the conditions, with duplex grades
Forta SDX 2507 and
Forta DX 2205 also exhibiting similar corrosion resistance combined with high mechanical strength and leaner alloying of volatile elements. In all cases, performance can be assessed with the help of PREN (Pitting Resistance Equivalent) and CPT (Critical Pitting Temperature) values.
Hot water and chlorides
Typical austenitic stainless steels such as 304L and 316L are susceptible to stress corrosion cracking in warm, chloride-heavy environments – generally at temperatures above 50°C. High-alloyed austenitic
Ultra grades however show much better performance and
Duplex stainless steels, thanks to their austenitic-ferritic microstructure, are extremely resistant in these conditions. The stainless steel grade selection depends on the conditions and can vary from the leanest –
Forta LDX 2101, right up to
Forta SDX 2507.
Weight savings and cost predictability with duplex solution
Compared to austenitic grades, duplex stainless steels are generally lean with volatile and expensive alloying elements such as nickel and molybdenum.
Forta LDX 2101 lean duplex is an extreme example of this: It's corrosion resistance is achieved mainly by the alloying of chromium and nitrogen, while it's nickel content is only 1.5%. Duplex grades have high mechanical strength, which enables considerable weight savings in pulp & paper industry applications – such as pressure vessels and various types of processing and storage tanks. As such, duplex grades make for optimal construction materials for capital investment projects that require cost predictability.
Figure: Lean duplex provides superior price predictability over 304L and 316L due to its lean alloying concept.