Metso turns to lean duplex to solve corrosion challenges in hydrometallurgical equipment
Robust materials are needed to withstand the corrosive environments and elevated temperatures experienced in hydrometallurgical processes. For example, equipment used to refine metals like copper, nickel and zinc might contain aggressive acids at high pressures and at temperatures greater than the boiling point of water. The need for reliable, cost-effective hydrometallurgy systems is also becoming ever greater due to the growing demand for materials such as lithium and cobalt that is fueled by the transition to electric vehicles and renewable energy.
While traditional options like carbon steel coatings and fiber-reinforced plastics have been used, companies operating in challenging environments are turning to duplex stainless steels for their corrosion resistance, high strength, and cost efficiency. These grades have been developed to combine the strength and performance of ferritic and austenitic stainless steels.
An early adopter is Metso, the Finnish minerals processing and metals refining Technology supplier. For some years it has worked with Outokumpu to advancing hydrometallurgy using innovative duplex and lean duplex stainless steels. These materials deliver durable, cost-effective, and sustainable solutions for harsh environments.
Ahmad Mardoukhi, Materials Engineer at Metso, says: “Metso is the only company able to provide complete processes for battery minerals extraction, to refine battery chemicals, and battery black mass recycling. Our sustainable solutions help customers reduce, for example, their CO2 emissions. As a materials engineer, I’m only convinced to select materials based on fact-based data. Lean duplex stainless steel, produced by Outokumpu, is a perfect example of a durable and fully recyclable material that we use in our equipment.”
Lean duplex proves effective in Metso’s OKTOP® reactor.
The advantages of high-strength duplex stainless steel are illustrated by Metso’s OKTOP reactor, as shown in Figure 1, designed for high-quality leaching, precipitation, and metal recovery. This reactor has been successfully used for solid-liquid, gas-liquid, and other reaction systems in leaching, oxidation, and reduction processes. The reactor also contributes to battery black mass recycling, where lithium-ion batteries are safely processed into reusable materials.
The typical structure of an OKTOP reactor includes a large stainless steel tank with welded baffles and mixer. The reactor is used for dissolution, intermediate storage, and as a feeding tank for autoclaves. The construction material depends on operating conditions, with Outokumpu Lean Duplex Forta LDX 2101® being the most common. In more demanding applications, Forta DX 2205 or super duplex Forta SDX 2507 are used.
For example, a zinc direct leaching reactor operates at ~103°C with strong sulfuric acid (>100 g/L) and high hydrostatic pressure. Forta SDX 2507 provides high corrosion and wear resistance, outperforming super austenitic stainless steels.
Experiments also show Forta LDX 2101 has good fatigue strength, making it a cost-effective alternative to carbon steel and more highly alloyed stainless steels in varying leaching environments.
A long-lasting and low carbon solution
Metso and other mining companies now prioritize both performance and sustainability when selecting materials. Our low-carbon production plays a key role in reducing emissions. Figure 2 compares materials and total carbon footprints for two Metso projects, showing that sourcing duplex stainless steel from Outokumpu cuts emissions to less than a third of the industry average. This demonstrates the significant environmental benefits of choosing sustainable materials for metal production.
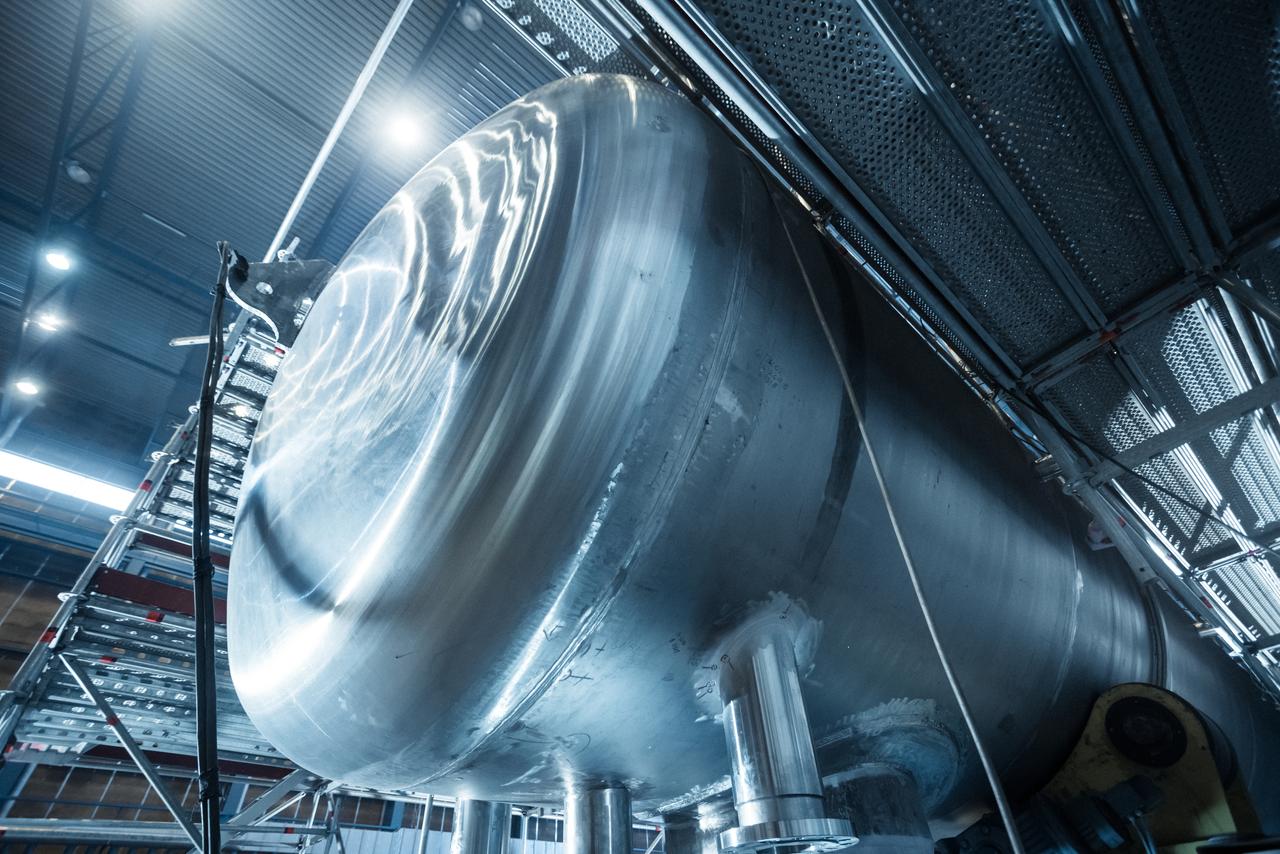
In summary, Metso uses duplex stainless steels for its hydrometallurgy equipment thanks to its corrosion resistance, high mechanical strength, cost-effectiveness and durability. Duplex grades offer high performance, reduced weight, stable pricing, and are mostly made from recycled materials using green energy, aligning with Metso’s sustainability goals.
Photos courtesy of Metso